Even heavy-duty engines need to be put on the test bench to verify the required exhaust gas quality at each operating point and its reduced fuel consumption. From 27 February to 5 March 2022, SYSTEMS & COMPONENTS, which takes place within the Agritechnica trade fair in Germany, will be showing the optimizations in fuel efficiency in the latest generation of off-highway engines. The technology providers that will be exhibiting in Hanover offer extensive system competence, encompassing intelligent exhaust gas after-treatment and injection technology for diesel, biodiesel or liquefied gas.
(DLG) Although combustion engines, particularly diesel engines, are widely regarded as being on the brink of extinction in public debate, they are far from finished in the off-highway sector, where they represent high availability, reliability and low operating costs with proven longevity under even the harshest of conditions. In addition to industry-specific factors, it is particularly efficiency and the legal requirements for reducing pollutants that are the technological driving forces. The progress achieved in engine development to optimize mobile working machines in terms of fuel consumption and emissions will be one of the central themes at SYSTEMS & COMPONENTS, which will be taking place for the fifth time in parallel with Agritechnica in Hanover, Germany.
Lower emissions at high output
Virtually all suppliers of conventional combustion engines will be present on site in Hanover with an extensive array of solutions to enable OEM customers to comply with the stringent exhaust emissions regulations according to European Off-Highway Stage V and US Off-Highway Tier 4 final. Many of these new developments are consistently pursuing the principle of downsizing: proven components for fuel injection (common rail system), engine and air management as well as exhaust gas after-treatment together with smaller engines form fuel-saving powerhouses.
Suppliers are paying great attention to the modularity of their engine systems. Components with flexible mounting enable different installation options and system integration in line with requirements. The versions differ, for example, due to fan attachments and belt-drives, cylinder head covers and oil pans made of plastic and aluminum, up to and including turbochargers with wastegate or charge pressure control with variable turbine geometry. Contrary to their diesel counterparts, engines running on natural gas are equipped with cooled exhaust gas recirculation. In order to comply with emission regulations, the engines are fitted with an exhaust gas after-treatment system consisting of a diesel particulate filter (DPF), selective catalytic reduction (SCR) and diesel oxidation catalytic converter (DOC).
With biomethane for climate-neutral mobility
However, the different requirements made on mobile machinery such as dumper trucks, mobile excavators, tractors or combine harvesters also mean that there is no common engine solution. In this context, openness to technology will be important keywords at SYSTEMS & COMPONENTS when assessing the portfolio of engines. Besides diesel engines, a range of other concepts such as parallel hybrid, range extender, plug-in hybrid and fully electric systems will therefore also be presented at the B2B platform in Hanover. Additional focus at the trade fair will be placed on alternative fuels, which are intended to smooth the way to climate-neutral mobility. Amongst others, natural gas engines designed specifically for off-road applications in agricultural and construction machines will also be on show. Under real operating conditions, these output around ten percent less carbon dioxide than diesel engines.
In this process, the use of biomethane is increasingly shifting into focus in agriculture, as demonstrated by the New Holland T6 Methane Power – the world's first volume production tractor running on 100% methane. In its interior, a six-cylinder engine from FPT Industrial with a displacement of 6.7 liters uses compressed (CNG), liquefied (LNG) or renewable (biomethane) natural gas and complies with the EU Stage V emissions standard, thanks to the use of a three-way catalytic converter. The first tractors are scheduled for delivery over the next few months of 2021, with an impressive number of pre-orders due to be produced and delivered this year. In the future, refueling will therefore be possible at the farm's own biogas plant, provided that a corresponding gas conditioner is available. If the plant additionally ferments liquid or solid manure, the CO2 balance can even be negative.
Synthetic fuels as a new option
Synthetic fuels offer a potential solution in the zero-carbon scenario that has been relatively overlooked thus far. Such fuels can be produced using regenerative electricity. The main advantage of these power-to-liquid-based e-fuels is their high energy density, particularly when compared to battery systems. The background to this is that, while small commercial vehicles in agricultural use can be fully electrified, this is a huge challenge for heavy-duty mobile working machines. Partial electrification of the drivetrain in parallel with smaller engines powered using synthetic fuels, is one possibility for achieving relevant CO2 reductions. One example of this is methanol, produced regeneratively, which could be used as a drop-in replacement for the off-highway sector. The challenge posed by e-fuels is their requirement for regenerative electricity for CO2-neutral electrolysis and that this is not available in sufficient quantities at present. This important aspect on the road to a climate-neutral future will be discussed by engineers and experts in the 'Future Lounge' expert forums at SYSTEMS & COMPONENTS.
For a long time, hydrogen has played a subordinate role in the development of CO2-neutral drive concepts in the off-highway sector. The complex conversion of other forms of energy to hydrogen appeared to too complex to achieve the goal. However, since the European Union launched the 'European Clean Hydrogen Alliance' (ECH2A) in July 2020, industry focus is shifting increasingly to this topic, and not without good reason since regeneratively produced hydrogen is not only suitable as a fuel for fuel cells but can also be used directly in combustion engines and gas turbines. Since hydrogen is a fuel that contains no carbon, only minimal emissions are incurred mainly from combusted lubricating oil. Thanks to its low exhaust gas temperatures, nitrogen oxide outputs are already below the limit values, even without exhaust gas after-treatment. Efficient, lean operation additionally results in a consumption advantage in comparison with conventional combustion engines.
Hydrogen engines are picking up pace
So what does the ideal hydrogen drivetrain for an excavator look like? SYSTEMS & COMPONENTS aims to answer this question with the engine and turbo engine adaptations necessary to achieve this. Engine manufacturer Deutz has already presented such a prototype as an alternative to fuel cell technology: the TCG 7.8 H2. The hydrogen variant of the six-cylinder in-line engine for agricultural machinery can also be used in various hybrid configurations in combination with electric drives. The recipe for success for CO2-free combustion engines consists of efficient injection, lean combustion, exhaust gas recirculation, turbocharging and a special hydrogen catalytic converter. A project being undertaken at the Institut für Kolbenmaschinen (Institute for Piston Engines) at the Karlsruhe Institute of Technology (KIT) is also exemplary in this context. It is investigating the potential of future combustion methods using the example of heavy-duty commercial vehicles. To do this, the hydrogen is injected , in a first phase, into the engine's intake manifold and then later, after converting the engine, directly into the cylinder. Through this process Institute Director Prof. Thomas Koch and his team of scientists are able to analyze the influence of mixture formation on combustion. The aim is to establish the future technology road maps for commercial vehicle drives on this basis and to determine the technical challenges involved in implementing hydrogen engines.
The engine mix of the future
The performance of modern off-highway vehicles is based on the reliable and precise operation of the engines. The diesel engine will remain the engine of choice in the technology mix for the foreseeable future, but it now has competition. Whether gas, hybrid or electric, as regards the guiding SYSTEMS & COMPONENTS theme of 'Green Efficiency – inspired by solutions', the solutions on show in Hanover will help to unite market requirements and emissions regulations.
SYSTEMS & COMPONENTS takes place within Agritechnica, the world's largest trade fair for agricultural machinery, in Hanover, Germany, from 27 February to 5 March 2022.
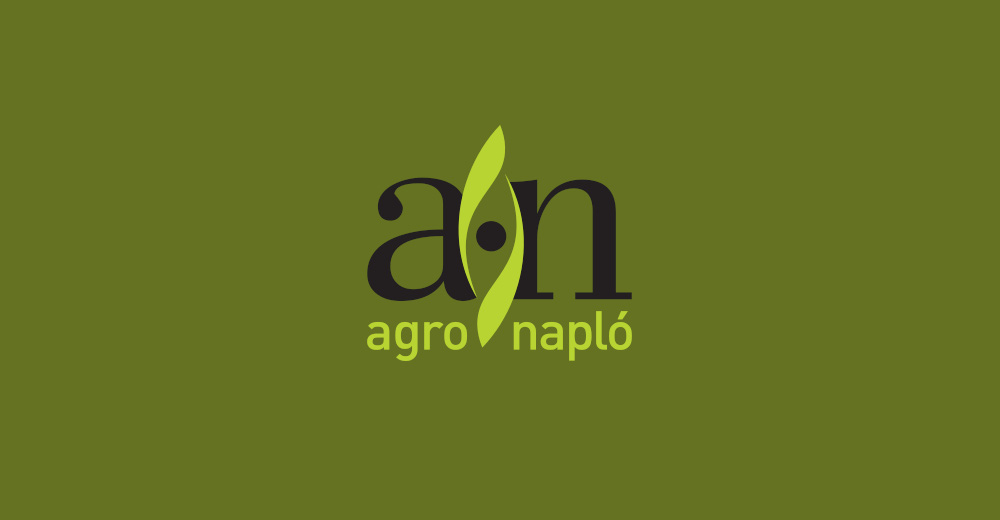
FPT Industrial brings the complete cycle of biomethane in agriculture to Agrishow 2023
FPT Industrial – a pioneer and leader in the development of alternative fuel engines with more than 20 years of experience and over 80,000 Natural Gas...